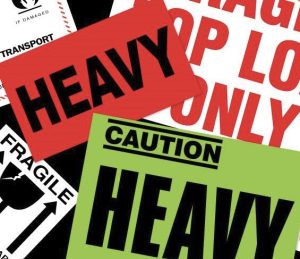
Fluorescent label printing is used to create labels that incorporate fluorescent materials. These labels are designed to result in vibrant and eye-catching visuals. The process involves incorporating fluorescent dyes or pigments into the ink or substrate used for printing, enabling the labels to fluoresce under appropriate lighting conditions.
The use of fluoro labels offers numerous benefits in various industries and applications. Here are some notable uses of fluoro label printing:
- Product Packaging and Branding: Fluoro labels are commonly employed in product packaging and branding to enhance shelf appeal and attract consumer attention. The vibrant and striking fluorescent colors stand out among other labels, helping products differentiate themselves and catch the eye of potential buyers.
- Industrial Applications: Fluoro labels find applications in various industrial settings, including manufacturing, logistics, and warehousing. These labels are often used for inventory management, organizing different products or components, and facilitating efficient tracking and identification. The high visibility of fluoro labels helps streamline processes and reduce errors.
- Safety and Warning Labels: Fluorescent labels are commonly used for safety and warning purposes. They help draw attention to important instructions, hazards, and precautions in environments where visibility is crucial. Fluorescent labels are often found on safety equipment, industrial machinery, chemicals, and electrical components to ensure compliance with safety regulations and protect personnel.
Fluorescent label printing offers a versatile and effective solution for a wide range of applications. The use of vibrant labels can improve brand recognition, enhance security measures, streamline processes, and provide visual cues in various industries, making them an invaluable tool in today’s dynamic market.
Some common names for Fluorescent Labels are:
- Fluorescent stickers
- Neon labels
- Glow labels
- Luminous tags
- Day-glo labels
- Hi-vis labels
- UV-responsive labels
- Radiant decals
- Light-emitting tags
- Illuminated markers
- Bright ink labels
- Fluoro labels
- Daylight-visible labels
- Highlight labels
- Luminescent stickers
- Vibrant fluorescent markers
These names are often used interchangeably to refer to labels that exhibit fluorescent properties, offering a range of options for different industries and applications.
PDQ Labels specialises in manufacturing custom fluorescent labels according to customer specifications. Here is an overview of how PDQ Labels typically produces custom fluorescent labels:
- Customer Consultation: PDQ Labels begins the process by engaging in a consultation with the customer. This step involves understanding the customer’s specific requirements, such as label dimensions, shape, design, color, quantity, and any special features or considerations. The consultation may occur through direct communication, online forms, or other channels.
- Material Selection: Based on the customer’s requirements, PDQ Labels selects the appropriate fluorescent label materials. There are various options available, including different adhesive strengths, paper or synthetic materials, and specific fluorescent properties. PDQ Labels can guide customers in choosing the most suitable materials for their intended application.
- Artwork and Design: Once the specifications are finalized, the customer provides or collaborates with PDQ Labels to create the artwork and design for the custom fluorescent label. This step involves incorporating the desired colors, graphics, text, logos, and any other specific elements. PDQ Labels may offer design services or work with the customer’s own design files to ensure accurate representation.
- Printing: PDQ Labels utilises specialised printing equipment and techniques to produce custom fluorescent labels. The selected fluorescent inks or substrates are used to create vibrant and high-quality labels that meet the customer’s specifications.
- Finishing and Die-Cutting: Once the labels are printed, PDQ Labels proceeds with the finishing process. This involves applying any additional features requested by the customer, such as varnishes, laminates, or coatings for protection or added visual effects. Die-cutting equipment is then used to cut the labels into the desired shape and size, following the specific specifications provided by the customer.
- Quality Control and Inspection: PDQ Labels conducts thorough quality control checks at various stages of production. This includes inspecting the printed labels for print clarity, label adhesion, and overall quality. Any labels that do not meet the required standards are rejected, ensuring that only the highest-quality custom fluorescent labels are delivered to the customer.
- Packaging and Delivery: The final step involves packaging the custom fluoro labels according to the customer’s preferences and delivering them in a timely manner, and they work with reliable shipping partners to ensure prompt delivery to the customer’s location.